Client: Norwood, Ontario
Solution: BNR
Background:
NORWOOD, ONTARIO ISAM™ (Integrated Surge Anoxic Mix) INCREASES PLANT CAPACITY WHILE REDUCING OPERATIONAL COST AND IMPROVING EFFLUENT QUALITY
The Township of Asphodel-Norwood (Township) is located in central-eastern Ontario in Peterborough County. Population growth in the community meant that the treatment capacity of the Norwood Water Pollution Control Plant (WPCP) needed to be increased from 0.19 MGD to 0.32 MGD average day flow (ADF).
The original WPCP included screening, grit separation, secondary treatment with a carousel-type extended aeration (EA) plant, and chlorine disinfection. Due to the necessary capacity increase, the effluent for the upgraded plant was required to meet a more stringent quality than the existing facility. In addition, the Township was considering the option of using final effluent as a source of irrigation water for a local golf course. After an assessment by the consulting engineer, the preferred upgrade option consisted of installing a second headworks screen followed by a Fluidyne ISAM™ sequencing batch reactor (SBR) to take the additional secondary flow and operate it in parallel with the existing secondary treatment process. In order to meet the more stringent phosphorous limit, aluminum sulphate is injected into the SBR to chemically precipitate phosphorus that is not removed biologically. The final secondary effluent is polished in a deep bed filter, followed by UV disinfection before being discharged to the Ouse River.
The upgraded plant was commissioned and began operating in October 2009. Once the ISAM™ SBR had been in operation for a couple of months, the Township decommissioned the extended aeration system and put the full flow through the ISAM™ SBR. This was due to the fact that there was sufficient treatment capacity for the existing total flow with the ISAM™ SBR. It was also determined that operating in this way would significantly decrease the operational and maintenance (O&M) costs of the WPCP. This was due to the fact that only one type of biological treatment process was operated, but also due to the ease of operating and maintaining the ISAM™ SBR system compared to the extended aeration system.
PLANT PERFORMANCE
Table 1 presents a summary of how well the Norwood WPCP has performed over the last three years. As the data shows, the plant has met all effluent quality requirements over this time period, and has been consistently well below the discharge limit since it has been operational. Comparing the data for 2009, when treatment was provided by the extended aeration process, with that provided in Table 1, the average effluent CBOD5, TSS and phosphorus concentrations are significantly lower with the ISAM process.
Table 1: AVERAGE OF INFLUENT AND EFFLUENT DATA FOR 2010 TO 2012
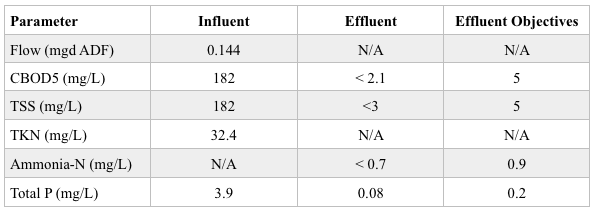
In terms of operation, with the old facility, operators were at the site 5 times per week. For the new plant they are there 3 times per week. Changes in operating procedures along with the ability to monitor the facility remotely, has reduced the need to be on site and allows for improved operational planning.
The ISAM™ SBR did not require the construction of a primary or secondary clarifier or a sludge digester. Therefore, the costs associated with the construction, interconnecting pipework, pipes and valves that are a part of having separate tanks for these processes is eliminated. In terms of capital cost, the upgraded plant actually ended up having lower capital costs than originally estimated. The estimated project cost was $7.20 million and the actual cost was $6.28 million.
Labor costs for the upgraded plant are also lower compared to the original, based on the significant reduction in operator attendance for the current plant, most of which is due to less time required to operate and maintain the biological treatment system. The estimated cost saving in labor is $10,000 per annum.
In terms of operational costs, there is actually an overall energy saving with the new plant associated with the transfer and digestion of sludge, as the primary sludge and waste activated sludge are stored and digested within the ISAM™ SBR, removing the O&M costs for settling, pumping and digesting sludge in separate processes.
The significantly lower sludge production with this process also reduces energy needs for sludge management as there is less to deal with. Energy savings also result from the use of a separate anoxic zone (SAM™) and during the anoxic conditions created in the SBR tank during the settling and idle phases. This is due to nitrate being used as the energy donor in place of oxygen during anoxic conditions, reducing the aeration demands for the aerobic treatment stage.
Although the upgrade essentially doubled the size of the facility along with increased capacity, the operating authority has been able to realize cost savings in operator time, biosolids hauling and improved effluent quality during high flow periods during spring run-off.
REFERENCES
Bukala, Z,; Sequire, J,; Aniye, M. (2013). BNR the Easy Way: Experience with an Integrated Surge Anoxic Mix (ISAM) SBR System.
Butler, R.C.; Merrill, M.S.; Finger, R.E.; Strutynski, B.; Newman, G. (1994). Low SRT Anaerobic Selector Pilot Plant Operation for SVI Control. Water Environment Federation, 67: 595 – 606.
Fluidyne Corporation. (2008). Special Activated Sludge System Works Well as Small Town`s First WWTP. Environmental Science and Engineering Magazine, May 2008.
Wang, L.K; Pereira, N.C.; Hung, Y.T. (2009). Biological Treatment Processes. Humana Press. Pittsfield, MA, USA.